When Emerald Packaging Inc. was established 60 years ago in Berkeley, Calif., the firm occupied 25,000 square feet and employed about 70 workers.
The company moved into a 50,000-square-foot building in Union City, Calif., in 1993 and now has a 200,000-square-foot facility there, 250 employees and is known as a cutting-edge provider of flexible packaging, said CEO Kevin Kelly.
Kelly's father, James, founded the company with three partners in 1963, but he bought them out 30 years later to form a family operation.
In 1975, he teamed up with Joe Gibbons, a packaging salesman from Salinas, Calif., who peddled Emerald's product throughout the Salinas Valley.
Then in 1979, Emerald Packaging developed a lettuce wrap that helped keep iceberg lettuce fresher longer.
“That's when we really started to take off,” Kelly said.
“We were the first to introduce a corn-based plastic for spinach in the 2000s,” he said.
And the company introduced potato bags made from potato starch in the 2010s.
Today, 95% of what the company makes is bags and roll stock for salads as well as celery, iceberg lettuce, spinach and other leafy greens.
The firm's latest launch is resealable lidding technology that is better than anything like it in the market, Kelly said.
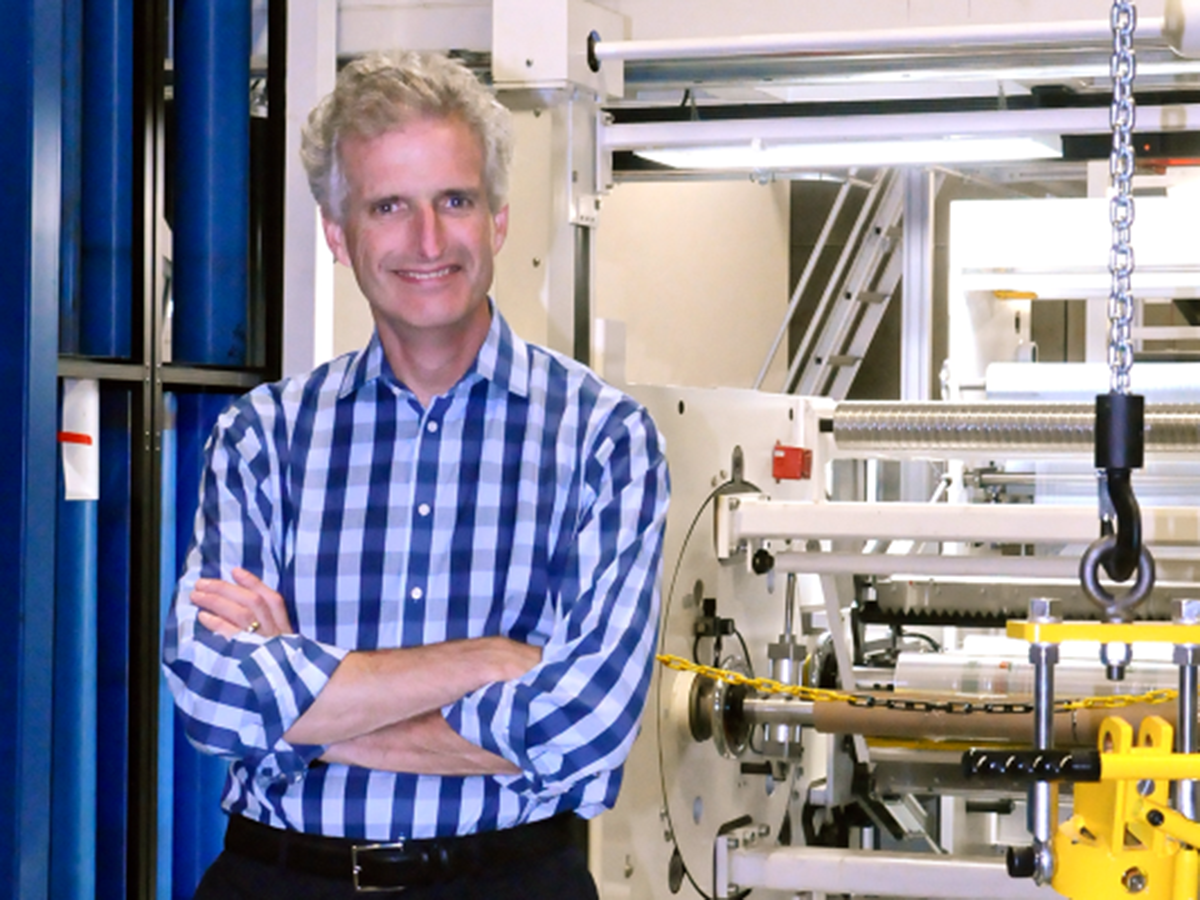
Another new product is scheduled for release by early next year.
“Our most recent push has been into post-consumer recycled resin,” he said. “We've developed a plastic that contains 30% PCR.”
The company will use PCR to manufacture a “revolutionary polyethylene bag” for field packing leafy greens for a major grower, he said.
“I'm excited about that because we'll finally be able to show market acceptance,” Kelly said.
Emerald Packaging has partnered with Circulus, a Modesto, Calif., startup which makes food-contact PCR. Emerald research turned it into a film structure capable of use in produce packaging, he said.
Compostable packaging can cost five or six times more than conventional packaging, he said. But the goal is to make Emerald's PCR packaging cost neutral.
Kelly said he has been working with Western Growers to encourage California lawmakers to pass legislation that would facilitate an infrastructure to produce more PCR material and better recycling programs that would reduce the amount of virgin plastic and help reduce greenhouse gasses.
Legislators seem to want to get rid of all packaging in the supermarket, Kelly said. But they're out of touch with consumers.
“The consumer trends are still toward packaging,” he said. “But they would like it to be more sustainable.”